European retailer partners with Iron Mountain to mine value from retired IT assets
There’s gold in retired IT assets, as one Scandinavian retailer discovered when it partnered with Iron Mountain Asset Lifecycle Management to replace more than 1,000 self-service ordering and payment stations in more than 170 locations across northern Europe.
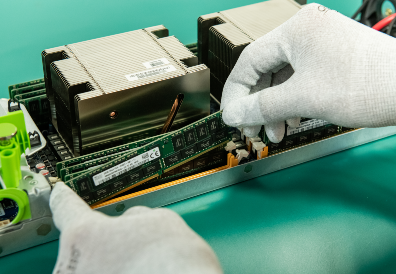
There’s gold in retired IT assets, as one Scandinavian retailer discovered when it partnered with Iron Mountain Asset Lifecycle Management to replace more than 1,000 self-service ordering and payment stations in more than 170 locations across northern Europe.
The company, a leader in sustainable business practices, decided in 2022 to upgrade its fleet of 15-year-old self-service terminals to maximise the potential to remarket components and responsibly recycle parts that couldn’t be resold. In a market with few comprehensive electronics recycling options, Iron Mountain brought everything to the table the retailer required: a fleet of secure vehicles for pickup, a global remarketing network, an assured chain of custody, expertise in material separation, world-class recycling facilities, and certified data sanitisation.
The timing was crucial. Retired equipment needed to be removed simultaneously while new terminals were installed to avoid disrupting the business. The 75-to-100-pound machines needed to be disconnected from pedestals and wall mounts without harming patrons. Iron Mountain’s secure transport professionals specialise in handling delicate electronics and choreographing complex logistics.
As new terminals were installed, the old equipment was palletised and secured in Iron Mountain vehicles. for transportation to Iron Mountain’s facility in Lulea, Sweden, which is certified under the Responsible Use and Recycling guidelines (R2v3), as well as multiple International Standards Organisation secure remanufacturing and disposal standards.
Value uncovered
Upon assessment there were plenty of remarketable components in the retired equipment. They included touchscreen displays, network switches, peripheral adapters, hard disks, embedded computers, graphics cards, and printers. Components were carefully removed, cleaned, tested and sanitised of all data. Iron Mountain’s global remarketing network then found buyers for the refurbished parts.
The effort yielded impressive results. About 93% of the touchscreens could be remarketed, with the rest responsibly recycled. All told, Iron Mountain Asset Lifecycle Management recovered more than one-third of the project's cost through resale. A portion of the proceeds was returned to the customer under a revenue-sharing agreement.
The European Union’s strict data privacy requirements made data security a priority. Incoming equipment was thoroughly scrubbed of data using Iron Mountain’s proprietary data sanitisation platform, Teraware™. Iron Mountain’s secure chain of custody provided complete compliance assurance at every step of the process, with an end-to-end audit trail to provide full visibility for the customer. Equipment that couldn’t be remarketed was responsibly recycled.
The project was completed in six months with no business downtime. The customer was excited to offer a new self-service experience with the peace of mind of knowing its commitment to sustainable practices was preserved.
Featured services & solutions
IT Asset Disposition: remarketing, recycling, and media destruction
Enhance security, improve sustainability, and protect your brand reputation with our ITAD services
Asset Lifecycle Management
ALM helps protect not only your data and the environment, but also your bottom line
Rethink sustainability
At Iron Mountain, we strive to be our customers’ most trusted partner for protecting and unlocking the value of what matters most to them in innovative and socially responsible ways
Related resources
View More Resources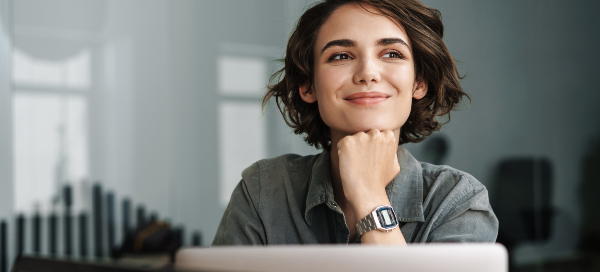
Iron Mountain at a glance
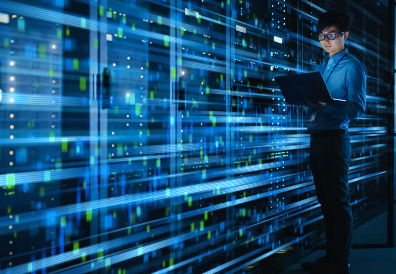